Unlocking the Potential of Local Plastic Moulding Manufacturers Near Me
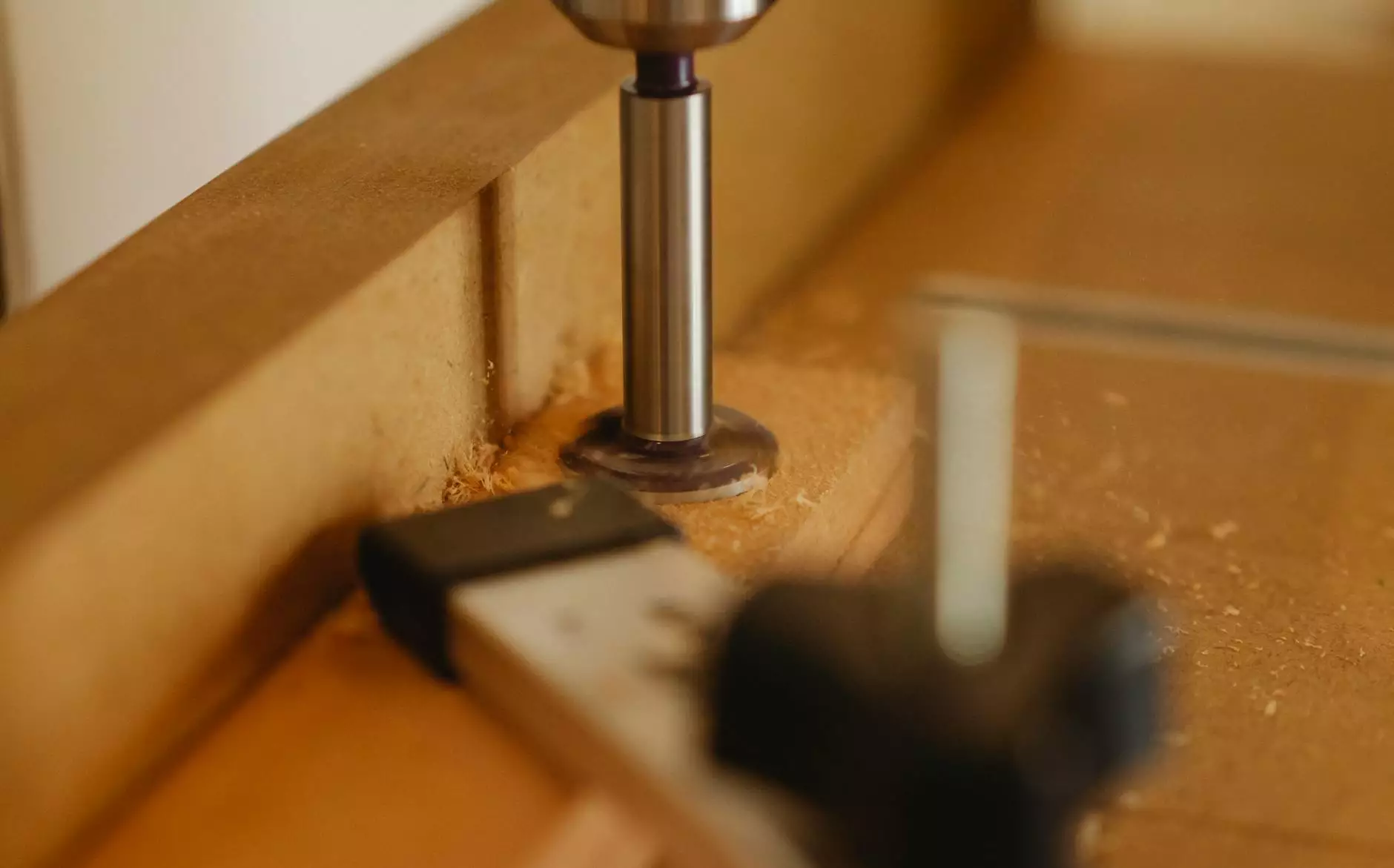
In today's fast-paced business environment, having reliable suppliers and manufacturers is crucial for success. When searching for plastic moulding manufacturers near me, you want to partner with quality-driven companies that understand your industry needs. In this comprehensive guide, we will explore the world of plastic moulding, focusing on key aspects like industry applications, choosing the right manufacturer, and the specific advantages of local partnerships. We aim to provide you with the knowledge you need to make informed decisions for your business.
The Importance of Plastic Moulding in Modern Manufacturing
Plastic moulding is a versatile and efficient manufacturing process that allows businesses to create complex parts and products at scale. This technique is used across various industries, including:
- Electronics: From casings for smartphones to intricate components in circuit boards, plastic moulding plays a vital role in electronics manufacturing.
- Medical Supplies: The healthcare sector relies on plastic moulding for durable and sterile components, ensuring the safety and efficiency of medical devices.
- Automotive: Automobile manufacturers utilize plastic moulding for everything from lightweight parts to cosmetic finishes, contributing to fuel efficiency and aesthetics.
- Consumer Goods: Everyday products, including household items and packaging, often come from moulded plastics.
Understanding Different Types of Plastic Moulding Processes
When exploring plastic moulding manufacturers near me, it's essential to familiarize yourself with the various types of plastic moulding processes available:
1. Injection Moulding
This is the most common form of plastic moulding. The process involves injecting molten plastic into a mould, allowing it to cool and solidify into the desired shape. Injection moulding is ideal for high-volume production due to its efficiency and precision.
2. Blow Moulding
Blow moulding is primarily used for creating hollow plastic parts, such as bottles and containers. It involves inflating a heated plastic tube until it fills a mould, and then cooling it to create a sturdy product.
3. Thermoforming
In thermoforming, sheets of plastic are heated and then formed into various shapes using vacuum or pressure. This method is often used for packaging and manufacturing trays, lids, and other shallow containers.
4. Rotational Moulding
This technique is suitable for producing larger items and involves rotating a mould filled with plastic resin, which coats the inside and forms a uniform thickness as it cools. Rotational moulding is often used for items like containers and playground equipment.
Why Choose Local Plastic Moulding Manufacturers?
Partnering with local plastic moulding manufacturers offers numerous advantages that can enhance your business operations:
1. Improved Communication
When you work with manufacturers nearby, you can benefit from face-to-face meetings and quicker responses to inquiries or issues. Clear communication leads to better collaboration and fewer misunderstandings.
2. Reduced Transportation Costs
Local sourcing can significantly lower transportation expenses, helping you to manage your budget more effectively. The reduced carbon footprint associated with local shipping is also beneficial for the environment and can enhance your company's sustainability image.
3. Shorter Lead Times
Working with manufacturers in your region can decrease lead times for production and delivery, allowing your business to remain agile and responsive to market demand. Quick turnaround times are essential for maintaining a competitive edge.
4. Supporting Local Economy
By choosing local plastic moulding manufacturers, you contribute to the growth of your community’s economy by supporting local jobs and businesses. This not only enhances your company’s reputation but also builds stronger community ties.
How to Select the Right Plastic Moulding Manufacturer
Choosing the right manufacturer can be daunting. Here are a few key factors to consider when searching for plastic moulding manufacturers near me:
1. Experience and Expertise
Look for manufacturers with substantial industry experience. A well-established company will have refined its processes and knowledge over time, enabling them to produce high-quality products consistently.
2. Specialization in Your Industry
If you’re in the electronics or medical supply sectors, it’s crucial to find manufacturers familiar with your industry’s specific requirements and standards. Specialized companies are more likely to understand regulatory compliance and quality control processes necessary for your products.
3. Technological Capabilities
Evaluate the technological advancements of the manufacturer. State-of-the-art equipment and innovative techniques can lead to better product quality and efficiency. Inquire about their capabilities in mould design, production speed, and secondary operations like assembly.
4. Quality Assurance Practices
Quality is paramount in plastic moulding, especially for industries like electronics and medical supplies. Ensure that the manufacturer has stringent quality assurance processes in place to guarantee that products meet the highest standards.
5. Client References and Case Studies
Request client references and case studies to gauge the manufacturer’s reliability and the scope of their previous projects. Positive testimonials can provide insight into their track record and customer satisfaction levels.
Looking to the Future: Trends in Plastic Moulding
The plastic moulding industry is constantly evolving, driven by technological advancements and changing market demands. Here are some trends to watch:
1. Sustainable Practices
As environmental concerns grow, more manufacturers are turning to sustainable materials and processes. This includes using recycled plastics and focusing on eco-friendly production methods.
2. Advanced Automation
Automation technologies are becoming integral to plastic moulding, enhancing efficiency and consistency. Robotics and AI are increasingly utilized to streamline production and reduce human error.
3. Customization and Personalization
Today's consumers often demand customized products. Manufacturers that can offer personalization in their designs and capabilities stand to gain a competitive advantage.
4. Increased Focus on Quality and Compliance
With tight regulations in sectors like electronics and healthcare, manufacturers are focusing more on quality control and compliance practices. This ensures products meet all necessary standards, minimizing the risk of recalls and liability issues.
Conclusion: Embrace the Local Advantage
Finding top-tier plastic moulding manufacturers near me is crucial for businesses in the electronics and medical supplies sectors. By choosing local partners, you can enhance your operational efficiency, reduce costs, and build lasting relationships within your community. Understanding the various moulding processes, trends in the industry, and how to select the right manufacturer will equip you with the tools needed to make informed decisions that propel your business forward.
At Nolato, we pride ourselves on being at the forefront of plastic moulding technology, offering tailored solutions that meet complex industry needs. Partner with us and experience the benefits of exceptional quality and rapid service. Let us help you transform your ideas into reality with precision and excellence.