Exploring the Benefits of Lathe Parts Made in China
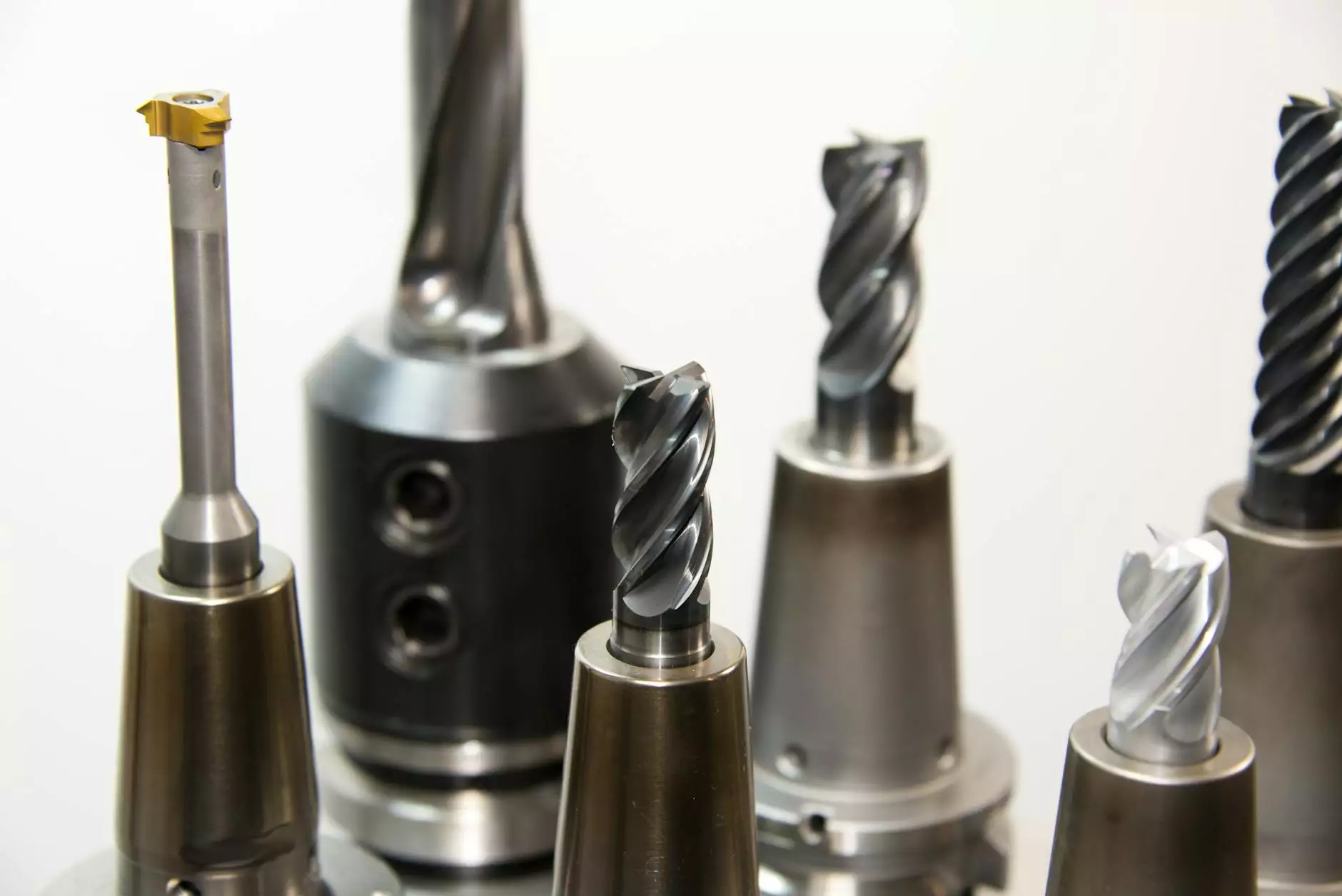
In the realm of manufacturing, sourcing components like lathe parts made in China has become increasingly popular due to the country's robust industrial infrastructure and competitive pricing. China has positioned itself as a global leader in metal fabrication, providing a myriad of benefits for businesses that require high-quality components at affordable prices. This article delves deep into the advantages, processes, and considerations when choosing lathe parts from China.
Why Choose Lathe Parts Made in China?
When it comes to procurement, especially in the metal fabrication industry, businesses must consider quality, cost, delivery times, and after-sales service. Here are the key reasons why lathe parts made in China are favored by numerous manufacturers around the globe:
1. Cost Efficiency
One of the most significant advantages of buying lathe parts from China is cost efficiency. The following points highlight how Chinese manufacturing keeps costs low:
- Low Labor Costs: China has a vast labor force with relatively low wages compared to Western markets, which significantly reduces production costs.
- Economies of Scale: Chinese manufacturers often operate on a large scale, allowing them to spread costs over a larger volume of products.
- Access to Multiple Suppliers: The competitive landscape encourages manufacturers to keep prices low while maintaining quality.
2. High-Quality Standards
Despite the perception that lower costs equate to lower quality, this is not always the case in Chinese manufacturing. In fact:
- International Certifications: Many manufacturers adhere to ISO 9001 and other international quality standards, ensuring their products maintain high quality.
- Advanced Technology: Continuous investment in technology and innovations allows Chinese manufacturers to produce sophisticated and precise products, including lathe parts.
- Strict Quality Control: Many factories implement robust quality assurance processes to ensure each part meets the required specifications.
3. Diverse Manufacturing Capabilities
China's metal fabrication industry is incredibly diverse, providing a wide range of lathe parts suitable for various applications. Some notable aspects include:
- Custom Manufacturing: Many suppliers specialize in custom fabrications, allowing buyers to request specific designs and dimensions.
- Wide Range of Materials: Options include aluminum, stainless steel, brass, and more, giving buyers flexibility in material selection based on their project needs.
- Innovative Designs: Utilizing advanced software and technology, manufacturers can create innovative and complex part designs.
4. Quick Turnaround Times
Another critical factor that enhances the appeal of sourcing lathe parts from China is the ability to meet deadlines:
- Efficient Production Lines: Many manufacturers have optimized their production lines for speed without compromising quality.
- Large Workforce: The vast workforce allows for multiple shifts, further accelerating production and order fulfillment.
- Established Supply Chains: A well-developed infrastructure facilitates the timely procurement of raw materials and delivery of finished products.
Understanding the Manufacturing Process of Lathe Parts
To fully appreciate the benefits of lathe parts made in China, it’s essential to understand the manufacturing process involved. Here’s a step-by-step overview:
1. Design and Prototyping
The initial stage involves creating detailed designs and prototypes. Manufacturers often collaborate with clients to finalize specifications, ensuring that the final product meets or exceeds expectations. Utilizing CAD (Computer-Aided Design) software is common, allowing for precision and flexibility in design.
2. Material Selection
Choosing the right materials is crucial. A wide variety of metals are available, and manufacturers assist clients in selecting based on cost, durability, and specific requirements. Popular materials for lathe parts include:
- Aluminum: Lightweight and corrosion-resistant.
- Stainless Steel: Offers excellent strength and resistance to corrosion.
- Brass: Known for its machinability and electrical conductivity.
3. Machining Process
Once materials are selected, the machining process begins. This can include:
- Turning: Rotating the workpiece against a cutting tool to achieve the desired shape.
- Milling: Using rotary cutters to remove material, often for more complex shapes.
- Grinding: Final processes to ensure parts achieve the required surface finish and tolerances.
4. Finishing Touches
After machining, parts may undergo various finishing processes to enhance durability and appearance, such as:
- Coating: Applying protective finishes, including anodizing or plating.
- Polishing: Improving surface finish for aesthetic or functionality purposes.
5. Quality Assurance
Before shipping, each product goes through rigorous testing and quality control checks. This ensures compliance with international standards and customer specifications.
Challenges and Solutions When Sourcing from China
While there are numerous benefits to sourcing lathe parts made in China, there are also challenges that buyers may face. Here are some common issues and their solutions:
1. Communication Barriers
Language differences can lead to misunderstandings. To mitigate this:
- Ensure that suppliers have English-speaking representatives.
- Utilize clear, concise specifications and drawings to minimize miscommunication.
2. Quality Consistency
Quality can vary across manufacturers. To ensure consistency:
- Conduct thorough due diligence and research before selecting a supplier.
- Request samples to verify quality before placing large orders.
3. Intellectual Property Concerns
Concerns about intellectual property theft exist when partnering with overseas manufacturers. Consider the following:
- Use non-disclosure agreements (NDAs) when sharing sensitive designs.
- Work with reputable suppliers that have a track record of respecting IP rights.
Conclusion
In conclusion, sourcing lathe parts made in China offers substantial advantages, including cost-effectiveness, high-quality manufacturing, and efficient production timelines. As the global market continues to evolve, understanding the intricacies of Chinese manufacturing becomes vital for businesses striving to maintain a competitive edge. By navigating potential challenges and choosing the right partners, companies can leverage the immense capabilities of Chinese metal fabricators like deepmould.net for their manufacturing needs.
Call to Action
If you are considering sourcing lathe parts for your business, do not hesitate to reach out to experts at deepmould.net. Our extensive experience in metal fabrication ensures you get the best quality lathe parts made in China that align with your business goals.