Unlocking Efficiency with Rapid Prototyping Plastic Injection Molding
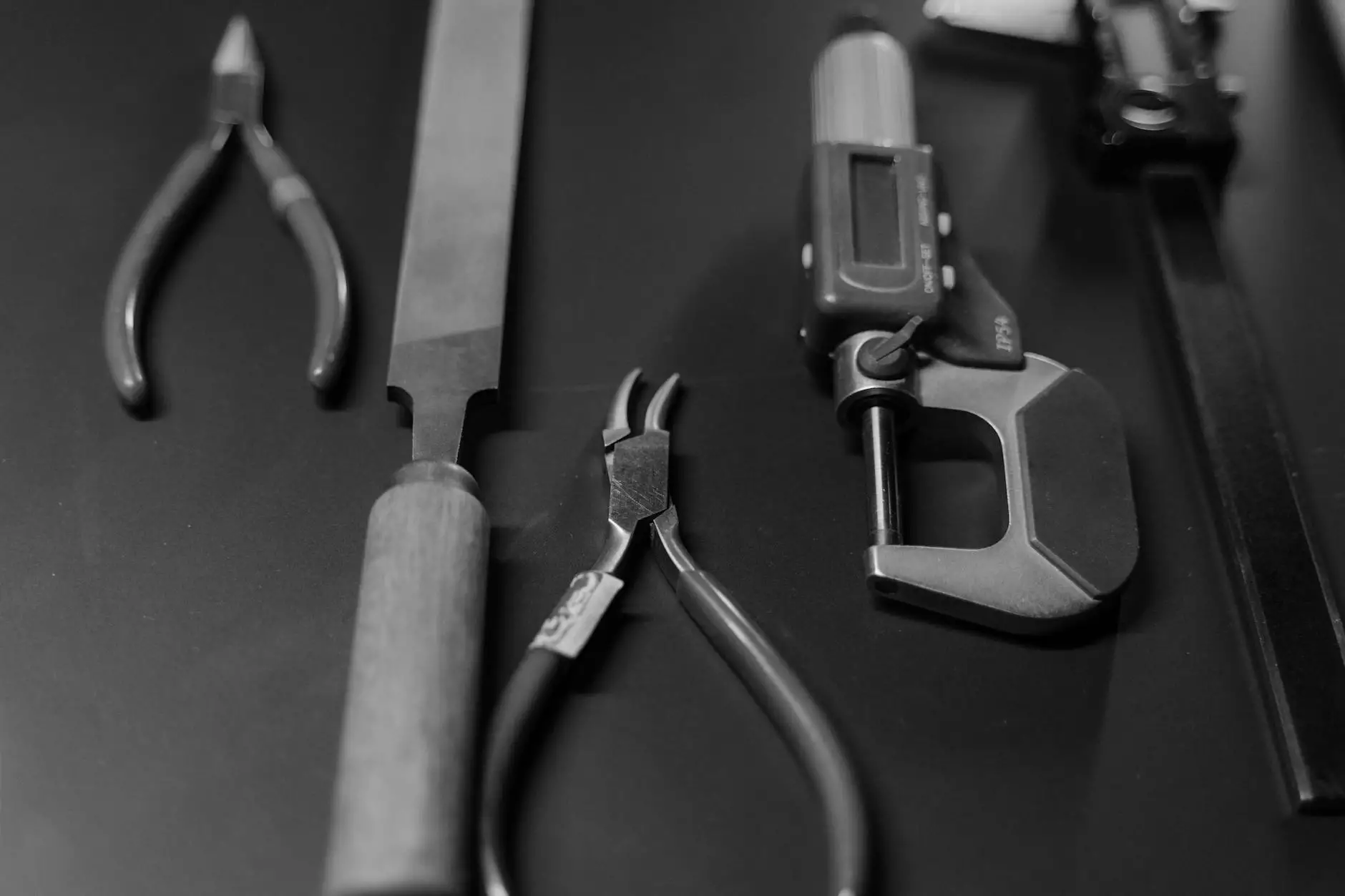
In today's fast-paced manufacturing landscape, the ability to innovate quickly and efficiently is more critical than ever. One of the most transformative techniques in this arena is rapid prototyping plastic injection molding. This method offers businesses the opportunity to create high-quality prototypes at an accelerated pace, significantly reducing lead times and enhancing product development cycles.
What is Rapid Prototyping Plastic Injection Molding?
Rapid prototyping plastic injection molding combines the principles of rapid prototyping and the traditional injection molding technique. It allows designers and engineers to produce a physical representation of their design in a fraction of the time it would take using conventional methods. This process involves creating a mold quickly using various advanced technologies and then injecting plastic materials to form the desired components.
The Process Explained
The process of rapid prototyping plastic injection molding can be broken down into several stages:
- Design Phase: Engineers use CAD software to create a digital model of the product. This design will serve as the basis for the prototype.
- Mold Creation: Using techniques such as CNC machining or 3D printing, a mold is created based on the CAD design.
- Material Selection: Appropriate plastic materials are chosen based on the requirements of the prototype, including durability, flexibility, and finish.
- Injection Molding: The selected plastic is injected into the mold under high pressure, allowing it to take the shape of the prototype.
- Curing and Finishing: After cooling, the prototype is removed from the mold, and any necessary finishing touches are applied.
Benefits of Rapid Prototyping Plastic Injection Molding
The integration of rapid prototyping plastic injection molding comes with numerous advantages that can greatly impact a business's bottom line and product quality. Here are some of the most notable benefits:
1. Speed and Efficiency
Time is money in the manufacturing industry. Rapid prototyping drastically reduces the time needed to produce initial prototypes. With this method, businesses can quickly iterate their designs, leading to enhanced development timelines and faster go-to-market strategies.
2. Cost-Effective Production
While traditional injection molding can involve high upfront costs due to the complexity of molding processes, rapid prototyping plastic injection molding minimizes these expenses by allowing for shorter runs of prototypes without the need for extensive tooling. This flexibility makes it a more cost-effective option for small batch productions.
3. Enhanced Design Validation
The ability to produce prototypes rapidly allows teams to conduct real-world testing sooner in the product development process. By evaluating physical prototypes, businesses can identify design flaws early and make necessary adjustments, greatly reducing the risk of costly changes later in production.
4. Material Diversity
An impressive range of materials can be utilized in rapid prototyping plastic injection molding. From thermoplastics to reinforced plastics, the choice of materials allows manufacturers to closely match their prototypes to the final product specifications.
5. Improved Communication and Collaboration
Physical prototypes enhance communication between teams, clients, and stakeholders. Visualizing a three-dimensional object facilitates discussions and feedback, enabling a collaborative approach to product development.
Applications of Rapid Prototyping Plastic Injection Molding
Various industries harness the power of rapid prototyping plastic injection molding for numerous applications, including:
- Aerospace and Automotive: Durable and lightweight prototypes assist in the design of critical components.
- Medical Devices: Rapid prototyping allows for the quick development of functional medical equipment.
- Consumer Goods: Brings innovative designs to market rapidly, addressing consumer needs effectively.
- Electronics: Streamlines the development of electronic housings and components.
Challenges and Considerations
While rapid prototyping plastic injection molding presents numerous benefits, businesses must also consider the potential challenges:
1. Initial Setup Costs
Although the production of prototypes can be cost-effective, the initial setup and mold creation may require a significant investment, particularly for complex designs.
2. Engineering Expertise
Having skilled engineers and designers is vital to ensure the success of the rapid prototyping process. Inadequate knowledge can lead to design errors or ineffective testing.
3. Material Limitations
Not all materials may be suitable for every application. Businesses need to carefully select materials that will best meet their prototypes' functional and aesthetic requirements.
Future Trends in Rapid Prototyping Plastic Injection Molding
The world of manufacturing is ever-evolving, and the future of rapid prototyping plastic injection molding is no different. Here are some trends that are likely to shape this field:
1. Advancements in 3D Printing Technologies
As 3D printing technology continues to improve, the prototyping process will become even more streamlined, allowing for faster mold production and enhanced design capabilities.
2. Integration with AI and Machine Learning
Artificial Intelligence (AI) and machine learning will likely play a more significant role in optimizing designs and predicting material performance, leading to fewer trials and errors during prototyping.
3. Sustainable Practices
The push for sustainability in manufacturing will drive the exploration of eco-friendly materials and practices in rapid prototyping. Businesses will increasingly seek ways to reduce waste and improve energy efficiency in their processes.
Conclusion
In summary, rapid prototyping plastic injection molding is revolutionizing the way businesses approach product development. By significantly reducing time and costs while improving design accuracy and collaboration, this method is proving to be a game-changer in various industries. Organizations that leverage this powerful technique will not only enhance their innovation capabilities but will also position themselves competitively in the marketplace. As manufacturing technologies continue to advance, the applications and benefits of rapid prototyping will only broaden, paving the path for a future of efficiency and excellence in production.
For more information on how to implement rapid prototyping plastic injection molding into your business strategy, visit deepmould.net and explore our services tailored to meet your manufacturing needs.