Unlocking the Potential of a Lathe Parts Factory
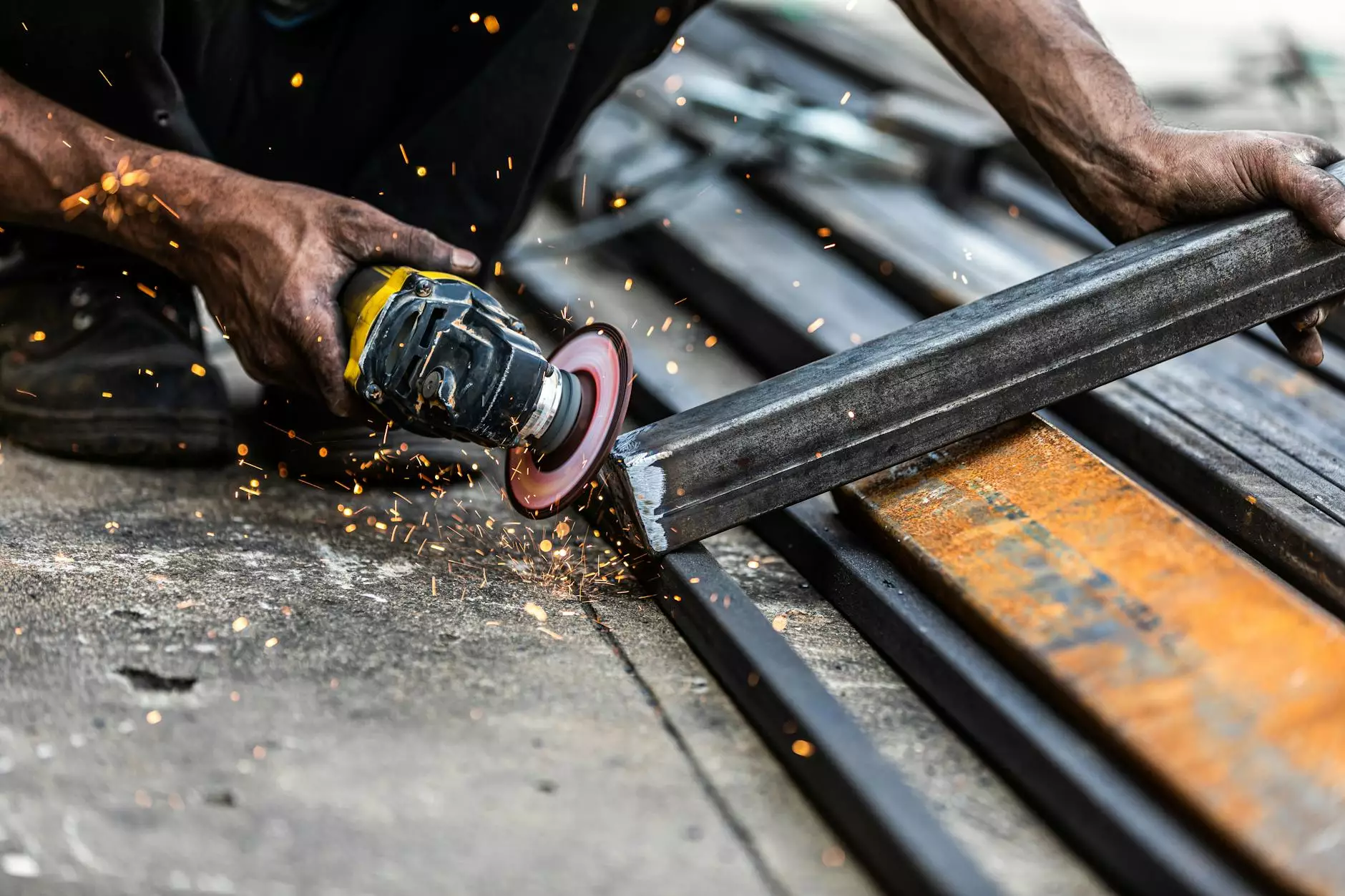
In today's fast-paced manufacturing industry, lathe parts factories stand as pillars of innovation, delivering precision-engineered components essential for various applications. From aerospace to automotive, the significance of these establishments cannot be overstated. In this article, we will explore the operational intricacies, the technology involved, and the various advantages of utilizing a lathe parts factory.
The Role of Lathe Parts Factories in Metal Fabrication
Lathe parts factories play a crucial role in metal fabrication, a process that converts raw materials into desired shapes and sizes through various machining techniques. Lathes are among the most fundamental machines in manufacturing, and understanding their operation is key to appreciating the functions of a lathe parts factory.
What is a Lathe?
A lathe is a machine tool that rotates a workpiece to perform various operations such as cutting, sanding, drilling, or deformation. By allowing the workpiece to rotate against cutting tools, lathes enable the manufacture of cylindrical parts with high accuracy. The types of lathes widely used in factories include:
- Engine Lathes: Ideal for general-purpose machining.
- CNC Lathes: Automated lathes that use computer numerical control for precision.
- Toolroom Lathes: Designed for high precision and small-scale jobs.
- Specialized Lathes: Customized for niche requirements.
Understanding the Operations of a Lathe Parts Factory
The operation of a lathe parts factory is complex and involves several stages to ensure accurate and efficient production of lathe parts. Here’s a detailed breakdown of these processes:
1. Material Selection
Choosing the right material is paramount in producing quality lathe parts. Common materials include:
- Aluminum: Lightweight and corrosion-resistant.
- Steel: Offers high strength and durability.
- Brass: Known for its machinability and aesthetic appeal.
- Plastic: Used for specific applications where metal is not required.
2. Design and Engineering
The design phase involves creating precise specifications using Computer-Aided Design (CAD) software. This process is critical as it determines how the lathe parts will be manufactured and how they will function in their intended applications. Here, engineers work closely with design teams to ensure that all parts meet the required specifications.
3. Machining Process
Once the designs are finalized, the actual machining process begins. Modern lathe parts factories utilize advanced cutting tools and machinery to produce high-precision components. The machining process typically involves:
- Turning: The workpiece is rotated against a stationary cutting tool to remove material.
- Facing: Used to create a flat surface on the workpiece.
- Drilling: Creating holes in the workpiece.
- Tapping: Producing internal threads for fastening.
4. Quality Control
Quality control is an ongoing process throughout the manufacturing task. Lathe parts factories implement strict quality assurance protocols, including:
- Dimensional Inspection: Ensuring components meet precise measurements.
- Material Testing: Checking for strength, hardness, and other properties.
- Functional Testing: Verifying that parts perform as intended under operational conditions.
Advantages of Utilizing a Lathe Parts Factory
There are numerous advantages to engaging with a lathe parts factory, particularly for businesses involved in metal fabrication.
1. Precision and Accuracy
One of the most significant benefits is the high level of precision achievable through modern machining. CNC lathes, for example, provide tolerances that traditional methods cannot match, ensuring that every part produced fits perfectly into its assembly.
2. Cost-Effectiveness
Despite initial setup costs, a lathe parts factory can be highly cost-effective in the long run. Automated processes reduce labor costs and increase production efficiency, leading to a lower price point for end products.
3. Versatility
Lathe parts factories can produce a wide range of components for various industries, making them a versatile choice for sourcing essential parts. From unique prototypes to mass production, these factories are equipped to handle diverse manufacturing needs.
4. Expertise and Experience
Working with a lathe parts factory grants businesses access to skilled machinists and engineers who understand the complexities of metalwork. Their expertise ensures that the best practices are followed, further enhancing product quality.
Integrating Innovative Technology in Lathe Parts Factories
The evolution of technology has dramatically changed the landscape of lathe parts manufacturing. Today’s factories employ cutting-edge innovations that improve efficiency and enhance product quality.
1. Automation and Robotics
Automation has streamlined operations in lathe parts factories. Robotics can perform repetitive tasks with speed and precision, allowing skilled workers to focus on more complex assignments.
2. Advanced Software Solutions
Modern factories use advanced software to plan, monitor, and optimize the manufacturing process. This includes ERP (Enterprise Resource Planning) and MES (Manufacturing Execution Systems) that facilitate effective resource management.
3. 3D Printing Technology
Although traditional machining remains essential, 3D printing is increasingly becoming a complementary technology in lathe parts production. It allows factories to create prototypes and small batches quickly, reducing time to market.
Challenges Faced by Lathe Parts Factories
Despite their advantages, lathe parts factories encounter several challenges that they must navigate to remain competitive.
1. Supply Chain Disruptions
Global supply chain issues can affect the availability of raw materials, leading to delays in production schedules. Factories must build robust relationships with suppliers to mitigate these risks.
2. Skill Gaps in Workforce
The rapidly advancing technology and methods require a skilled workforce. Factories may struggle with skill gaps, necessitating investment in training and development programs.
3. Rising Energy Costs
As energy prices continue to rise, factories must find ways to operate sustainably and more efficiently. Implementing energy-efficient machinery and optimizing processes can help reduce costs.
The Future of Lathe Parts Factories
The future of lathe parts factories looks promising, with innovations driving the industry towards greater efficiency, sustainability, and adaptability.
1. Sustainability Initiatives
Many factories are embracing green manufacturing practices, reducing waste, and minimizing environmental impacts. This shift not only serves the planet but also resonates with increasingly environmentally-conscious consumers.
2. Customization and Personalization
The demand for customized parts is on the rise. Lathe parts factories are focusing on flexible manufacturing systems that allow for the quick alteration of production lines to meet specific customer needs.
3. Industry 4.0
The integration of IoT (Internet of Things) and smart technologies is set to revolutionize the manufacturing sector. Factories equipped with smart sensors and data analytics will be better positioned to anticipate production challenges and enhance efficiency.
Conclusion
In conclusion, the lathe parts factory is a crucial component of the metal fabrication industry, providing precision-engineered components that empower a multitude of sectors. As technology advances and the industry evolves, these factories will continue to play an indispensable role in meeting the demands of modern production. For businesses looking to leverage the benefits provided by lathe parts factories, the focus should be on collaboration with experienced manufacturers such as Deep Mould, who are committed to quality and innovation in every project.